Importance of Proper SS
Flange Installation
1. Leak Prevention
Proper installation techniques ensure a tight, secure seal, preventing costly and hazardous leaks that can compromise process safety and environmental compliance
2. Structural Integrity
Correctly torqued flanges maintain the structural integrity of piping systems, reducing the risk of catastrophic failures and downtime.
3. Corrosion Mitigation
Careful surface preparation and gasket selection help mitigate corrosion, extending the lifespan of SS flanges and the overall system.
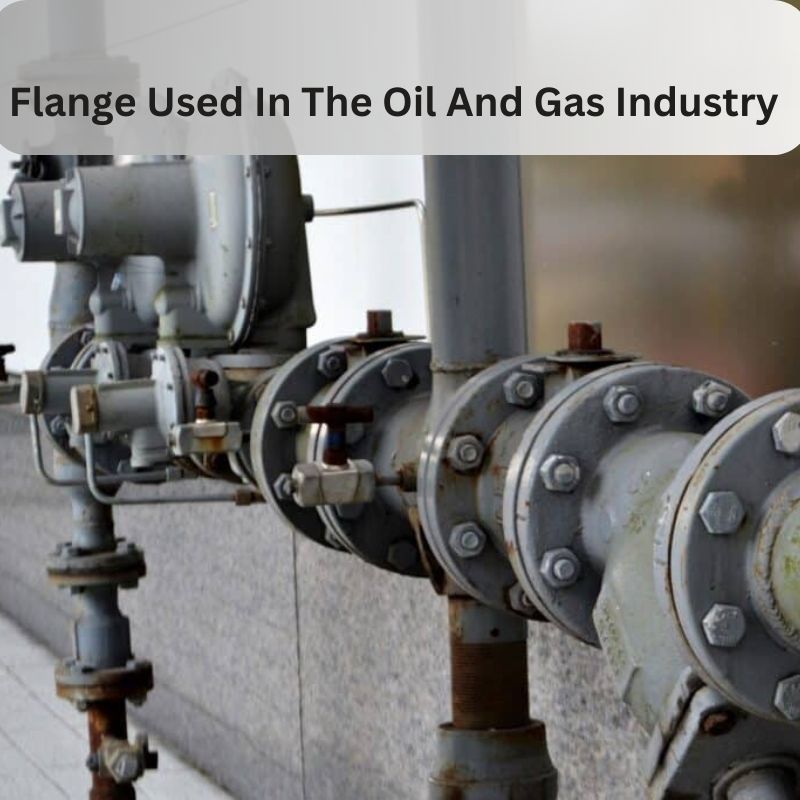
Selecting the Right SS Flange for the Application
Material Com patibility
Choose SS flanges that are
compatible with the specific fluids,
temperatures, and pressures
present in your gas and oil
operations to ensure long-term
performance and safety.
Dimensional Considerations
Carefully measure your piping
system and select flanges with the
appropriate bolt patterns, face-toface dimensions, and other critical parameters to ensure a proper fit.
Regulatory Compliance
Ensure your SS flange selection
meets all relevant industry standards and regulations, such as ASME B16.5 or API 605, to maintain compliance and avoid costly issues.
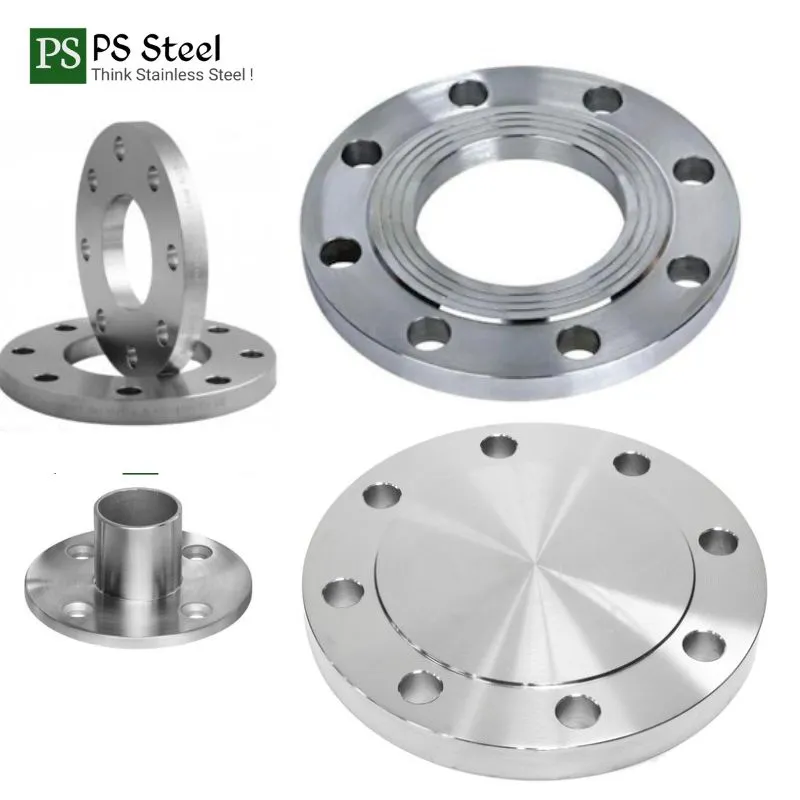
Preparing the Flange Surface for Installation
1 Thorough Cleaning
Remove any dirt, rust, or other contaminants from the flange faces to provide a clean, smooth mating surface for the gasket.
2 Surface Finish
Ensure the flange faces meet the recommended surface finish requirements, typically 125-250 micro-inches, to achieve a proper seal.
3 Damage Inspection
Carefully inspect the flange faces for any nicks, scratches, or other damage that could compromise the seal and lead to leaks.
4 Lubrication
Apply a thin, even coat of approved lubricant to the bolt threads and under the bolt heads to ensure proper torque is achieved.
Sequence
Tighten the bolts in a star or crisscross pattern to evenly distribute the clamping force and prevent distortion of the flange faces.
Incremental Tightening
Gradually tighten the bolts in multiple passes, using a calibrated torque wrench to achieve the specified torque value.
Incremental Tightening
Gradually tighten the bolts in multiple passes, using a calibrated torque wrench to achieve the specified torque value.
Ensuring Proper Gasket Placement and Compression
Gasket Selection and Placement
Choose a gasket material that is compatible with the media and operating conditions, and carefully center the gasket between the flange faces to prevent leaks.
Compression Requirements
Tighten the bolts to the recommended torque value to achieve the proper gasket compression, ensuring a tight, secure seal without over-compressing the gasket.
Troubleshooting Leaks
If a leak occurs, check the gasket for damage or improper placement, and retorque the bolts to the specified value. If the issue persists, consider replacing the gasket

Mitigating Corrosion Risks in SS Flange Installations
Corrosion Monitoring
Regularly inspect SS flanges for signs of corrosion, such as discoloration, pitting, or cracking, and address issues promptly to prevent failures.
Cathodic Protection
Implement cathodic protection systems to minimize electrochemical corrosion and extend the lifespan of SS flanges in harsh environments.
Isolation Kits
Use insulating gaskets, sleeves, and washers to electrically isolate SS flanges from dissimilar metals, preventing galvanic corrosion.
Protective Coatings
Apply specialized coatings, such as epoxy or fluoropolymer, to the flange surfaces to provide an additional barrier against corrosion.
Troubleshooting Common SS Flange Installation Issues
Leaks
Verify proper gasket selection, surface preparation, and bolt torqueing techniques. Retorque or replace the gasket as needed.
Flange Distortion
Ensure even tightening of the bolts, check for damaged or warped flanges, and consider using flange alignment tools.
Bolt Failure
Inspect for signs of corrosion or overtightening, and replace any damaged bolts. Use the recommended lubricants and torque values.
Gasket Degradation
Select a gasket material that is compatible with the operating conditions, and replace it at the first sign of wear or deterioration.
Troubleshooting Common SS Flange Installation Issues
1. Proper Selection
Choose SS flanges that are compatible with your specific operating conditions and meet all relevant industry standards.
2 Careful Installation
Follow best practices for surface preparation, gasket placement, and bolt torqueing to ensure a tight, secure seal.
3 Corrosion Mitigation
Implement corrosion-resistant measures, such as isolation kits and protective coatings, to extend the lifespan of your SS flanges.
4 Proactive Maintenance
Regularly inspect and maintain your SS flanges to identify and address any issues before they lead to leaks or system failures.
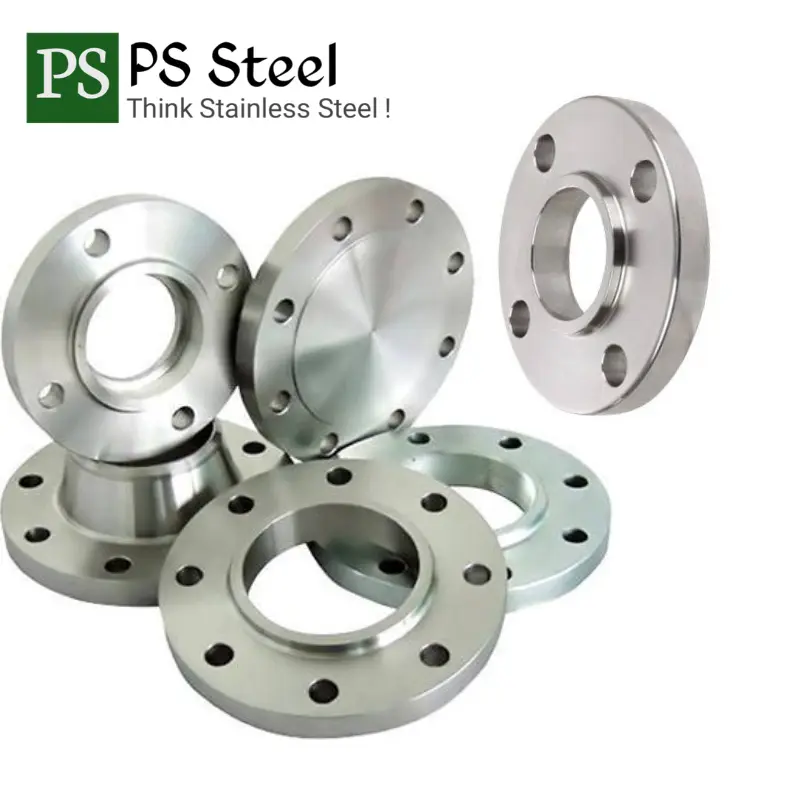
- All
- Pipe & Tube
- SS Flanges
- SS New Products
- SS Pipe
- SS Sheet
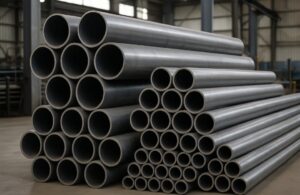
Best Mild Steel Pipe free Quotes | Ms pipes Online
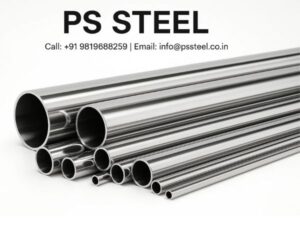
SS Pipes for Railing Weight Chart List by PS Steel
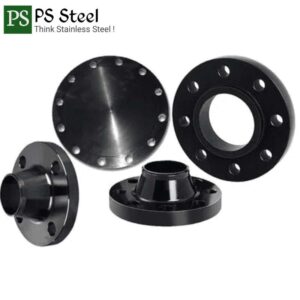
MS Pipe Flanges Dimension Chart in Kg
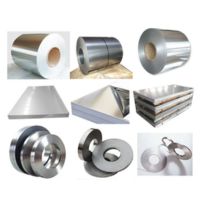
Steel Plate | Steel Chequer Plate Best Price Supplier
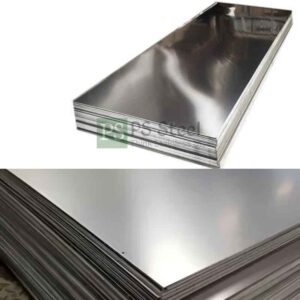
SS Plate Weight Chart in Kg
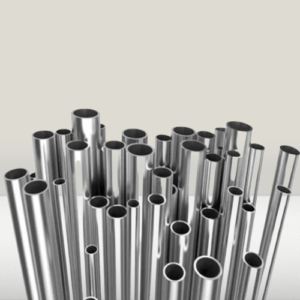
SS Pipe Tube Weight Chart List

SS Pipes for Food and Beverage Industry Supplier
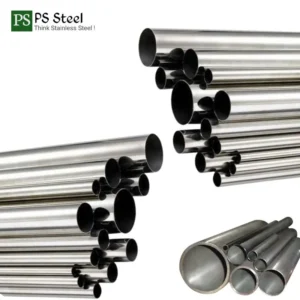
Review SS Flanges Installation Best Practices in the Gas and Oil Industry.